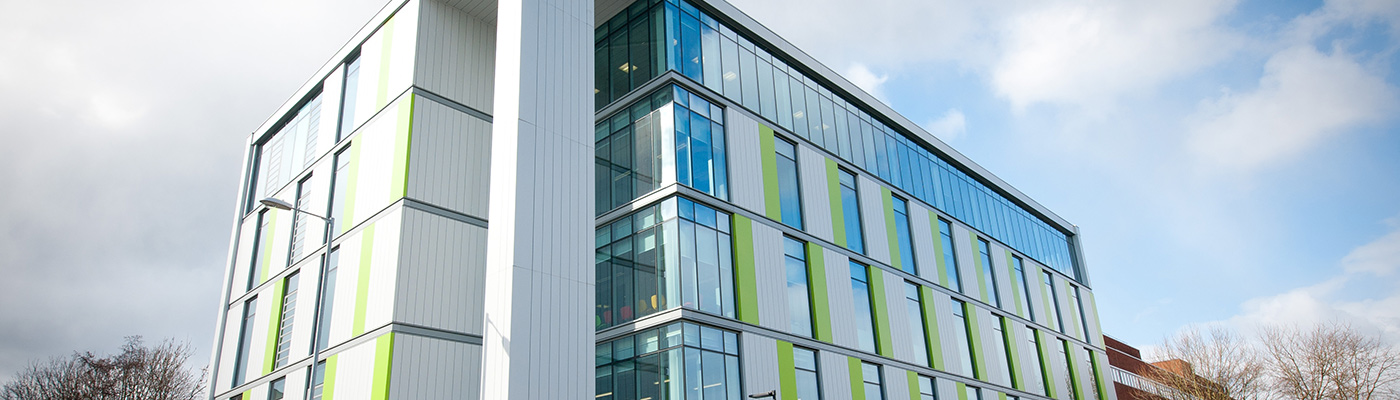
Facilities
Our Department is home to world-class research facilities, benefiting our researchers, students and collaborators.
Industrial Hub for Sustainable Engineering
Discover our new Hub, which brings cutting-edge innovations in sustainable processes to commercial application by the industry, and aims to train the next generation of chemical engineers with the knowledge and business skills to bring about a low-carbon, sustainable future.
We boast an impressive range of laboratory space, dedicated computer suites and a pilot scale area containing a range of large-scale industrial processing equipment, all housed in our £12 million James Chadwick Building.
This development is one of the largest and best equipped of any European university, and our pilot plant, laboratory and workshop facilities are available to industrial collaborators, along with the services of an excellent team of academic and support staff.
We are working hard to ensure we are able to provide safe access to these facilities in line with the latest government advice. The safety and wellbeing of our staff and students is our highest priority and we will be providing health and safety briefings as part of your induction.
Our equipment
We host a full suite of leading analytical equipment and computing facilities, some of which is listed below. This is not an extensive list, but a general overview and there are many more specialist and bespoke pieces of characterisation tools in individual academic groups.
Experimental equipment
Spectroscopy
- Fourier transform infra-red hyperspectral imaging microscopy
- Fourier transform infra-red Attenuated Total Reflectance (FTIR-ATR)
- Raman spectroscopy
- Raman optical tweezers
- Gas and high performance liquid chromatography and mass spectroscopy
- Inductively coupled plasma energy dispersed x-ray spectrometry
- UV-spectrophotometers
- X-ray tomography
- X-ray photoelectron spectroscopy
Scattering
- Small and wide angle light scattering
Microscopy
- Optical microscopy
- Fluorescence microscopy
- Confocal microscopy
- Infra-res microscopy
- Environmental scanning electron microscopy
Thermal characterisation
- Thermal gravimetric analysis
- Differential scanning calorimetry (standard and micro)
Other
- Micro-fluidic chip production facilities
- Chemical sensors, including micro-milling and injection moulding, electron-beam coating, sensors for chemical and physical measurements.
- High content high throughput multiwall assay robot - momentum
- Automated cell culture - sonata
- Total carbon/nitrogen units
- Solvent characterisation equipment (ie. densitometer, viscometer, Karl-Fisher titrator) as well as a wide array of extraction facilities (Soxhlet, shaking incubators, microwave, solid phase extraction etc.)
- Temperature controlled orbital shakers
- Atmospheric glove box
- High current potentiostat
- Higher temperature furnaces
- Maximum bubble pressure tensiometer
- Force tensiometer
- Mastersizer
- Zetasizer
- Thermal imaging
- 3D printing facilities
- Inductively Coupled Plasma analysis (ICP)
- Particle size analysis
- Drop levitation
- Crystallisation equipment (including Crystal16, several batch and continuous crystallisers)
- Oscillatory rheometry
- Interfacial rheometry
- Langmuir trough
- Peptide synthesiser
- Range of bioreactors form the laboratory to the pilot scale
- Nitrogen adsorption BET
- Helium pycnometry
- Mercury porosimetry
Computational equipment
- Crystal structure prediction
- Ab initio modelling
- X-ray spectroscopy calculations
- Molecular dynamics
- Monte Carlo simulations
Unit operations
- Industrial mixing, 50 – 3000 litre
- Instrumented batch reactions
- High shear in-line mixing
- In-line high-pressure homogenizing emulsification
- Structured processing
- Pneumatic conveying
- Crystallisation Sedimentation
- Flocculation
- Continuous processing absorption
- Distillation (continuous and batch)
- Cleaning-in-place
- 
Gas sparging

- Froth floatation
- Reaction engineering
- Bio-processing
This list is not exhaustive, and facilities can be adapted to accommodate new operations as required.
Process analytical technology
A range of sensors and analysers is available for in situ, on-line and at-line measurements. These include but are not limited to:
- In situ process near-infrared, mid- infrared and Raman spectroscopy
- Process tomography
- Process NMR
- Particle image velocimetry
- On-line particle sizing and viscosity
- Sensors for monitoring process variables such as conductivity and turbidity
- Proprietary sensors and analysers, developed in-house for specialised applications
- Data analysis and modelling
Data analysis techniques already well-used within SCEAS include data integration, multivariate analysis and chemometrics. Multiscale modelling is also widely used, such as computational fluid dynamics and molecular dynamics.
Other facilities
The Department enjoys the use of an extensive range of other important facilities and maintains a strong presence in a number of research centres and institutes.
-
Electron Microscopy Centre
The Electron Microscopy Centre houses a suite of 22 electron microscopes, comprising 13 scanning electron microscopes, four dual beam focused ion beam microscopes (including one plasma focused ion beam) and five transmission electron microscopes. Atomic resolution imaging and simultaneous chemical mapping are achievable with the FEI Titan G2 80-200 scanning transmission electron microscope and the centre also boasts a full suite of environmental cell and in situ testing capabilities.
-
Manchester beamlines at Diamond
The University of Manchester has joined forces with Diamond Light Source, the UK's national synchrotron science facility, to produce a world-class imaging facility. This allows researchers in a wide range of fields to create high-quality 3D images of samples, including engineering components, biomaterials, fossils, organic materials and energy devices such as fuel cells.
Read more
-
Nuclear Magnetic Resonance (NMR) spectroscopy
Nuclear Magnetic Resonance (NMR) spectroscopy is a powerful, continually evolving analytical technique with wide applications in chemical, biological, pharmaceutical and medical sciences. This technique has made rapid strides over the last two decades, both in theory and in applications, and works in conjunction with modern computer and information technology. The breadth and quality of information attainable from NMR measurements makes it unique among spectroscopic tools.
-
Manchester X-ray Imaging Facility (MXIF)
The Manchester X-ray Imaging Facility provides academic and industrial users a suite of ten world-class complementary non-destructive 3D X-ray imaging instruments. MXIF enables researchers from a wide range of disciplines to analyse and characterise materials samples as large as 1m in diameter or to image with spatial resolutions of 1mm to 50mm using the highest resolution machines in the UK.
Read more
-
N8 High Performance Computing (N8 HPC)
N8 HPC currently offers a shared 'Tier 2' HPC facility underpinning world-class research, enabling collaborations between institutions and creating the opportunity to engage more effectively with business and the community. The computing capability and capacity available to leading researchers in the N8 universities provides a platform for sharing methodological and technical expertise, and creates new opportunities for business-facing collaborative research.
-
Computational Shared Facility (CSF)
The CSF is a collection of servers joined together to form a large High Performance Computing resource for University researchers to run computationally-intensive calculations, simulations and problem analyses. It is built on a shared model, the expansion of which is funded by research groups. The service began in spring 2011 and is operated on behalf of the research community by IT Services.
Read more